Metallography is fundamental to understanding the microstructure of metals and alloys, providing critical insights into material properties and performance. However, metallographic analysis relies heavily on one key factor: sample preparation. A single flaw during this process can distort results, leading to incorrect interpretations and costly errors in applications ranging from aerospace to manufacturing.
Despite advancements in technology, sample preparation remains one of the most challenging aspects of metallography. Issues such as deformation during cutting, contamination during mounting, and surface irregularities during polishing continue to pose obstacles.
Common Obstacles in Sample Preparation
The path to successful metallographic analysis begins with flawless sample preparation. However, this journey is often hindered by several challenges that require meticulous attention and the right approach. Below are the most common obstacles faced during this critical process.
Sectioning Difficulties
One of the first steps in sample preparation is sectioning, where a representative portion of the material is cut for analysis. This step may seem straightforward, but it is fraught with challenges. Using improper tools or techniques can generate heat, leading to thermal damage and microstructural changes in the sample. Mechanical stress from cutting can also cause deformation, which obscures critical features like grain boundaries or phases during analysis.
By way of example, a poorly sectioned turbine blade could show inaccurate microstructural data, risking failure in high-stress environments. The solution lies in selecting the right cutting equipment, such as diamond saws or low-speed precision cutters, which minimize heat and stress during the process.
Mounting Challenges
After sectioning, the sample is typically mounted to make handling easier and protect its edges during subsequent steps. However, improper installation techniques can lead to several issues, such as poor edge retention or contamination. If the mounting resin or material interacts with the sample, it can alter the results, making it difficult to identify the original microstructural features.
A classic example is the use of unsuitable epoxy for a highly sensitive alloy, which could introduce unwanted residues. The use of high-quality, non-reactive mounting materials and thorough curing are necessary for maintaining sample integrity.
Grinding and Polishing Issues
Achieving a smooth, scratch-free surface is critical for accurate metallographic analysis, but this step is one of the most technically demanding. Improper grinding can leave deep scratches or introduce surface deformation, while insufficient polishing can obscure the finer details of the microstructure.
In failure analysis of a fractured steel component, surface scratches from inadequate polishing might hide critical inclusions or cracks. Using a systematic approach with progressively finer abrasives and following established polishing protocols can result in a mirror-like finish that reveals every detail without distortion.
Best Practices to Overcome Preparation Challenges
Overcoming metallography sample preparation challenges starts with understanding the root causes and implementing best practices at each stage. The first step, sectioning, is the foundation of the process. Poor sectioning practices, such as using incorrect cutting tools, can introduce thermal damage and deformation, distorting the material’s true microstructure. To address this, laboratories should utilize advanced tools like low-speed precision cutters or diamond saws. These tools, designed to minimize heat generation and mechanical stress, guarantee that the sample remains representative of the original material. Regular calibration and maintenance of such hardness testing equipment further increases their reliability, reducing inconsistencies among different samples.
Mounting, the next critical step, often determines how well the sample withstands subsequent processes. Improper mounting can lead to contamination, poor edge retention, or even structural alteration. High-quality, non-reactive resins are essential to prevent interactions that could compromise the material. Additionally, automated mounting systems ensure consistent results, especially for samples with irregular shapes or delicate features. Many laboratories now employ hardness testing tools to assess the stability and uniformity of mounted samples, identifying potential flaws before progressing to the next stage.
Grinding and polishing represent perhaps the most technically demanding aspects of sample preparation. Achieving a flawless surface without scratches or deformation is vital for accurate microstructural analysis. The process requires the systematic use of progressively finer abrasives, each stage building on the previous to eliminate imperfections. Modern polishing systems with automation capabilities reduce operator variability and streamline the process, while advanced hardness testing equipment verifies surface integrity.
Advanced Techniques and Innovations in Metallography Preparation
The metallography field has seen a surge in technological advancements aimed at addressing long-standing challenges. One such innovation is the adoption of automated preparation systems, which have transformed grinding, polishing, and even etching processes. These systems are equipped with programmable settings to ensure consistency, reducing preparation times significantly. For example, an automated polishing system integrated with advanced hardness testing tools can measure the microhardness of the surface in real time, making sure that the sample meets predefined standards before moving to analysis.
Emerging technologies like ion beam polishing and cryo-preparation have also revolutionized how difficult materials are handled. Ion beam polishing is particularly effective for hard or brittle materials, such as ceramics or high-strength alloys. This technique removes surface material at the atomic level, creating a scratch-free finish without mechanical stresses. Cryo-preparation, on the other hand, is ideal for soft or ductile materials, as it freezes the sample to prevent smearing during grinding and polishing. These methods, when combined with state-of-the-art hardness testing equipment, enable laboratories to overcome material-specific challenges with increased precision.
In addition to these techniques, consumable advancements have played a significant role. Abrasives with nanometer-scale precision allow for finer polishing, while chemically engineered etchants provide better control during microstructural revelation. Case studies from leading industries have demonstrated the impact of these innovations. In one case, an aerospace manufacturer reduced sample preparation times by 30% and improved analysis accuracy by incorporating automated systems and next-generation abrasives.
The integration of automation and cutting-edge technologies has made metallography more efficient and reliable. By leveraging these tools and techniques, laboratories can overcome traditional challenges and set new benchmarks for sample preparation and quality. These advancements make certain that microstructural analysis of materials meets modern industries’ exacting demands, providing insights that drive innovation and safety.
Advancing Precision in Metallography Sample Preparation
Metallography sample preparation is both an art and a science, requiring precision, expertise, and the right tools to reveal intricate microstructures. From the initial sectioning to the final polishing, each step presents unique challenges that, if left unaddressed, can compromise the integrity of the analysis. However, by implementing best practices and leveraging advanced technologies such as automated preparation systems and innovative hardness testing equipment, laboratories can overcome these obstacles with confidence.
Ongoing advancements in tools and techniques, such as ion beam polishing and cryo-preparation, have improved sample preparation quality and efficiency but also set new benchmarks in the field. These innovations empower industries to make more informed decisions, resulting in greater safety, reliability, and performance.
With the rapid pace of technological change in today’s world, the ability to adapt and embrace cutting-edge solutions will define success in metallography. By prioritizing precision and adopting advanced methods, professionals can continue to unlock material secrets, driving progress and innovation for all industries.
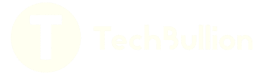
Leave a Reply